Plastic granulators are essential equipment in the processing of plastic materials. They play a pivotal role in recycling and manufacturing industries by transforming plastic waste or raw materials into granules for reuse. Here’s an overview of the primary functions and classifications of plastic granulators:
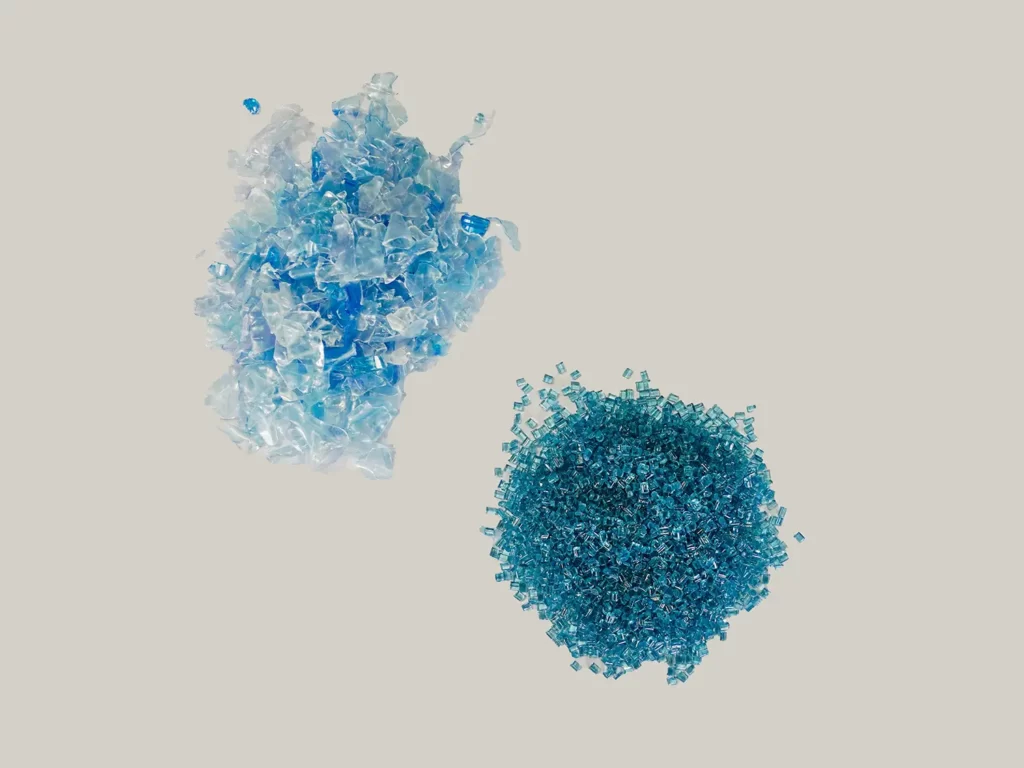
Helstu aðgerðir
- Melting and Mixing: Plastic granulators melt solid plastic into a liquid state and mix it with other components for uniformity.
- Filtering: They remove impurities and contaminants to ensure the quality of the produced plastic granules.
- Cooling and Solidifying: After molding through dies, the molten plastic is cooled and solidified into granular form.
- Cutting: The machines cut the long strands of plastic into granules.
- Þurrkun: Removing moisture from the granules to ensure they are dry for storage and transportation.
Types
- Single Screw Granulators: Utilize a single screw to propel the melting and extrusion of plastic, suitable for processing various general-purpose plastics.
- Twin Screw Granulators: Feature two parallel or intermeshing screws, offering better mixing, venting, and degassing, ideal for complex plastic formulations.
- Ring Water Granulators: Use a circular water trough for cooling and cutting, suitable for thermally sensitive materials.
- Vatnshringur skurður granulators: Perform cutting in a water environment, ideal for materials requiring specific granule shapes and sizes.
- Strand Cutting Granulators: Produce granules through stretching and cutting, commonly used in polymer processing.
The choice of a plastic granulator depends on the type of plastic to be processed, production capacity, and quality requirements of the granules. Proper selection and use of granulators are crucial for enhancing the efficiency of plastic recycling and production processes.
Fjölföldun er ekki leyfð án leyfis.:Rumtoo vélar » Skilningur á plastkornum: Aðgerðir og gerðir